Cerium Modified Nanocrystalline SmFeO3 for Ethanol Sensing
1Department of Physics, Smt. Radhabai Sarda Arts, Commerce and Science College, Anjangaon Surji 444705, Maharashtra State, India.
2Department of Physics, Arts, Science and Commerce College, Chikhaldara 444807, Maharashtra State, India.
Corresponding Author E-mail: rbmankar@gmail.com
DOI : http://dx.doi.org//10.13005/ojc/400206
Article Received on : 05 Jan 2024
Article Accepted on :
Article Published : 06 Mar 2024
Reviewed by: Dr. Abt Almasoodi
Second Review by: Dr. Masoud Salavati Niasari
Final Approval by: Dr. Malinee Sriariyanun
Presently, detection of ethanol has become essential in various fields due to its adverse effects on human beings. For selective detection of ethanol, chemiresistive gas sensors are widely investigated. Modified ABO3 type perovskites have shown their potential in the fabrication of chemiresistive gas sensors. In present work, SmFeO3 perovskite oxide based thick films were fabricated and surface modified with cerium by simple dipping technique. The structural properties of the samples were studied by Field EEmission Scanning Electron Microscopy (FE-SEM) and Energy Dispersive X-ray spectrometer (EDS). The results of FE-SEM indicate that average grain size was in nano range and Ce-modified SmFeO3 films were comparatively more porous than pure SmFeO3 film. This porous nature of film favors gas sensing mechanism. The results of EDS suggest that Ce was deposited on the surface of SmFeO3 films. The gas response of pure SmFeO3 film was tested towards LPG, CO2, NH3, H2, C2H5OH, Cl2, and H2S gases and observed that SmFeO3 film exhibited good response to ethanol (C2H5OH). Among modified samples, Ce-modified SmFeO3 film (dipping time 5 min) exhibited excellent ethanol sensing properties such as , maximum response (16.87 at 1000C ), response time (24 sec), recovery time (34 sec), excellent stability, and good selectivity towards ethanol. Thus Ce-modified SmFeO3 is a potential material in the fabrication of ethanol sensor. The impacts of Ce modification on the gas sensing performance of the SmFeO3 sensor ware discussed in detail.
KEYWORDS:Gas response; SMO gas sensor; SmFeO3; Surface modification; Sol-gel method
Download this article as:
Copy the following to cite this article: Mankar R. B, Kapse V. D. Ce Modified Nanocrystalline SmFeO3 for Ethanol Sensing. Orient J Chem 2024;40(2). |
Copy the following to cite this URL: Mankar R. B, Kapse V. D. Ce Modified Nanocrystalline SmFeO3 for Ethanol Sensing. Orient J Chem 2024;40(2). Available from: https://bit.ly/432kqh5 |
Introduction
Development of gas sensors for environmental monitoring has been an active area of research. Among various gas sensors, chemiresistive gas sensors have proved their potential in the detection of hazardous gases. Metal oxide semiconductors have been extensively studied as promising material for selective detection of gases 1-2. So far, n-type metal oxides semiconductors like ZnO, TiO2, SnO2, LaFeO3, and WO3 were frequently reported for chemiresistive gas sensors 3-7. They have high sensitivity, low cost and their sensing mechanism is well explained. On the other hand, p-type semiconductors have been relatively less explored for chemiresistive gas sensors. Exploitation of their interactions with target gas may lead to new sensors with enhanced properties.
SmFeO3 is p-type metal oxide semiconductor usually studied as a chemiresistive gas sensor material for the detection of oxidizing gases 8-11. It has an orthoferrite phase and ABO3-type perovskite oxide structure 8. Its resistance decreases in presence of ozone, oxygen, NO2, etc. and increases with exposure to reducing gases like ethanol, ammonia, etc. At low temperature, electrical conductivity of SmFeO3 is very small for both oxidizing and reducing gases which results in lack of response. Moreover, SmFeO3 is not stable due to the phase separation of Sm2O3 when exposed to reducing gases 12-13. Due to these two reasons, the applicability of SmFeO3 is limited to detection of oxidizing gases at higher temperature. Now, chemical stability and electric conductivity are related with cations at A and B sites in ABO3 type perovskite oxide. Therefore doping of SmFeO3 could be an effective approach not only to increase its electrical conductivity but also to use it under reducing conditions. Doping Co, Ni or Mg in SmFeO3 have been attempted to increase electrical conductivity of SmFeO3. But still there is a problem of stability in reduction conduction with these dopants since, Co-O, Ni-O and Mg-O bonds are weaker.
Ethanol is one of the most volatile and flammable gas 14. It is used in sanitizer, chemical industries and in industrial production. Different organs of the body including the brain can have serious some time permanent damage due to heavy ethanol drinking 15-16. Therefore, ethanol-monitoring is strongly required. SmFeO3 was reported for ethanol gas detection but optimal operating temperature was very high around 3700C 17,18. To reduce the optimal operating temperature, Ma Zhao et al. prepared Co-doped SmFeO3 and obtained maximum response to 300 ppm ethanol at lower optimal operating temperature 2150C 19. Cobalt doping improved electrical conductivity of SmFeO3 but reduced the chemical stability in the reducing environment. S. M. Bukhari et al. investigated that Ce doping in SmFeO3 improved the electrical conductivity and also prevent it from decomposing under a reducing environment 12. Thus Ce-doped SmFeO3 based gas sensor can be employed for detection of reducing gases like ethanol.
To the best of our knowledge, optimal operating temperature for doped SmFeO3 based ethanol gas sensor was above 2000C and only volume doping was investigated. Therefore in present work, attempt was made to modify SmFeO3 thick films by surface doping with cerium chloride using dipping method. The effect of Ce surface modification on ethanol gas sensing properties of SmFeO3 based gas sensor was investigated. The results depicted that Ce-modified SmFeO3 thick film with dipping time interval 5 min exhibited excellent ethanol response at reduced optimal operating temperature 1000C.
Material and Methods
Fabrication of Thick Films
Pure SmFeO3 powder was prepared by sol-gel method briefly described in our earlier publication20. The screen printing method was reported by many authors to fabricate thick films of semiconducting metal oxides 21-23. Thixotropic paste was prepared from the mixture of the fine powder of SmFeO3 and organic vehicles. This thixotropic paste was then deposited over the glass substrates by using a squeegee. After drying in air, the films were fired at 5000C for half an hour in Muffle Furnace.
Surface Modification of Thick Films
For surface modification, the dipping technique was adopted as reported by some researchers 24. 0.1 M aqueous solution of cerium chloride was prepared and to this solution SmFeO3 thick films were dipped. The dipping time intervals were 1 min, 3 min, and 5 min. These films are now identified as “Ce-surface modified SmFeO3 thick films”. They were dried in air for 48 hours before their firing in Muffle Furnace at 5500C.
XRD spectrum of SmFeO3 powder was studied to confirm its structure. To observe microstructure and compositions of the films, their FE-SEM with EDS spectra were recorded.
For examining the sensing properties of as prepared thick films, static gas sensing set-up was used which essentially consists of heater mounted on base plate and glass dome. Using silver electrodes, electrical contacts were made with thick film. During the experiment, the operating temperature was adjusted from room temperature to 4000C. Target gas of fixed concentration (60 ppm) was inserted inside the dome through gas inlet valve using syringe. In the test process, constant voltage was applied to the sensor and the current was measured using digital pico-ammeter in presence of air and the target gases. The gas response is determined from the relation
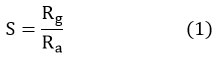
where, ‘Ra’ denotes sensor resistance in air and ‘Rg’ denotes its resistance in target gas at the same temperature 14. The selectivity of the film is tested against H2S, LPG, NH3 CO2, C2H5OH, Cl2, and H2.
Results and Discussion
X-Ray Diffraction Study
XRD spectrum of pure SmFeO3 powder was presented and discussed in detail in our earlier publication 20. The well defined sharp peaks of high intensity were obtained at 22.940, 25.650, 31.970, 32.710, 33.160, 46.730, 53.260, 58.910, 68.540, and 78.310. The corresponding lattice planes were respectively (101), (111), (200), (121), (002), (202), (311), (042), (242), and (421). The results well matches with the standard JCPDS card number 39-1490 and confirmed the perovskite phase with orthorhombic symmetry and Pnma space group. The average crystallite size was calculated using Scherrer’s formula
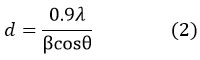
where ‘λ’ is wavelength of X-ray, ‘θ’ is diffraction angle and ‘β’ is Full Width at Half Maximum (FWHM). The average crystallite size was estimated as d=50.08 nm. The values of lattice parameters ‘a’, ‘b’ and ‘c’ were 5.604 Ǻ, 7.704 Ǻ, and 5.397 Ǻ respectively. The unit cell volume is calculated to be V=233.05 Ǻ3.
Morphological Analysis
Fig. 1 (A) is the FE-SEM image of pure SmFeO3. Fig. 1 (B – D) are the FE-SEM images of Ce-surface modified SmFeO3 with dipping time intervals 1 min, 3 min and 5 min.
![]() |
Figure 1: FE-SEM photographs for (A) SmFeO3 and Ce-modified SmFeO3 with dipping time intervals (B) 1 min, (C) 3 min, & (D) 5 min. |
All the images appear to be composed of large numbers of grains concluding the porous nature of the film. The agglomeration of few particles was also observed in Fig 1 (A). The size of SmFeO3 grains ranges from 53 nm to 131 nm. The FE-SEM images for Ce surface modified SmFeO3 thick films seem to be comparatively more porous. Therefore these films favor the adsorption and desorption processes in gas sensing mechanism. Ce particles might be deposited at the inner walls of basic SmFeO3 structure and the formation of Ceparticles on the surface of SmFeO3 can be confirmed from the EDS micrographs. Moreover, the number of small Ceparticles increases with increasing dipping time. The grain size was observed to be ranges from 55 nm to 69 nm in micrograph depicted in Figure 1(D).
Quantitative Elemental Analysis
![]() |
Figure 2: EDS images for (A) SmFeO3 and Ce-modified SmFeO3 with dipping time intervals (B) 1 min, (C) 3 min, & (D) 5 min. |
Table 1: Chemical compositions of pure and Ce-modified SmFeO3 thick films
Samples |
Sm (wt%) |
O (wt%) |
Fe (wt%) |
Ce (wt%) |
Pure SmFeO3 |
58.6 |
21.3 |
20.1 |
0 |
Modified SmFeO3 |
|
|
|
|
Dipping time- 1 min |
56.5 |
22.3 |
20.1 |
1.1 |
Dipping time- 3 min |
59 |
20.6 |
18.8 |
1.5 |
Dipping time- 5 min |
53.3 |
12.6 |
11.2 |
2.9 |
Fig. 2 presents the EDS spectra of pure and Ce-modified SmFeO3 which shows that Ce was deposited on surface modified SmFeO3 films along with Sm, Fe, and O. Moreover, no other impurities were detected in EDS images of as synthesized thick films thereby indicating purity of samples.
Chemical composition in pure and modified SmFeO3 is displaced in Table 1. It is observed that wt % of Ce increased with dipping time. In Ce modified samples, Ce molecules appear to substitute both Sm and Fe molecules.
Gas Sensing Performance
Response of pure SmFeO3 film was observed towards different target gases at 1000C and the results indicate that pure SmFeO3 film was sensitive to ethanol. To investigate the impact of Ce surface modification, gas response of pure and Ce surface modified SmFeO3 films towards 60 ppm ethanol gas was measured by changing the operating temperature from 320C to 4000C. Pure SmFeO3 thick film showed extremely small response (S=2.07) towards 60 ppm ethanol gas at 3000C. On the other hand, Ce-modified SmFeO3 thick films exhibited improved response and good selectivity for ethanol gas. The change in ethanol gas response according to the operating temperature and gas concentration was investigated for pure and Ce modified SmFeO3 thick films.
Gas Response and Operating Temperature
Fig. 3 shows ethanol gas response at different operating temperatures for all the four samples.
![]() |
Figure 3: Gas response for (A) SmFeO3 and Ce-modified SmFeO3 with dipping time intervals (B) 1 min, (C) 3 min, & (D) 5 min towards 60 ppm ethanol. |
For all the samples, the maximum ethanol gas response was recorded at particular operating temperature below and above which gas response decreased. Maximum response was 6.47 to 60 ppm ethanol for Ce modified SmFeO3 film (dipping time 1 min) and it was observed at 200 0C. For Ce modified SmFeO3 films with dipping times 3 min and 5 min, same optimal operating temperature was recorded as 100 0C. But, an improved response (S=16.87) was observed when dipping time was 5 min.
The gas response of SmFeO3 is due to the resistance change that happens in the adsorption and desorption 17-19. On the oxide surface, adsorption and desorption of ethanol molecules takes place simultaneously. When operating temperature was increase, more and more ethanol molecules were adsorbed and the sensor responses. However, when the temperature exceeds the optimum temperature, adsorption becomes slower than desorption and the redox reaction becomes less intense. Hence decrease in gas response is observed at high temperatures. Generally, resistance of SmFeO3 is affected by doping at Sm or Fe site because of the formation of oxygen vacancies. In Ce-modified SmFeO3 thick film, Ce occupies Sm or Fe or both sites which result in the formation of oxygen vacancies. This promotes oxygen adsorption.
Thus, Ce -modified SmFeO3 film with dipping time interval of 3 min exhibited excellent gas response to 60 ppm ethanol at 1000C.
Gas Response and Gas Concentration
Fig. 4 indicates the values of gas response at different ethanol gas concentration for Ce modified SmFeO3 sensor (dipping time 5 min) at 1000C.
![]() |
Figure 4: Gas response for Ce-modified SmFeO3 (dipping time 5 min) for different concentrations of ethanol gas at 1000C |
The increase in response, but in a different extent, with increasing ethanol gas concentration was observed. Below 20 ppm, the sensor is almost insensitive to ethanol. This low concentration region known as a cut off region indicates that only few ethanol gas molecules reacts with oxygen species. Hence sensor is almost insensitive to ethanol gas. Good linearity between gas response and ethanol concentration was obtained above 60 ppm because ethanol gas molecules reacting with chemisorbed oxygen species are optimum.
Selectivity of Ce-modified SmFeO3 Thick Film
![]() |
Figure 5: Selectivity of Ce-modified SmFeO3 thick film (dipping time 5 min) at 100 0C. |
Fig 5 illustrated the bar diagram indicating responses of Ce-modified SmFeO3 thick film at 1000C towards LPG, NH3, CO2, H2, C2H5OH, Cl2, and H2S gas. It is clear from the bar diagram that Ce-modified SmFeO3 thick film sensor (dipping time 5 min) was selective to C2H5OH gas against LPG, NH3, CO2, H2, Cl2, and H2S gases. This high selectivity to C2H5OH gas was attributed to Ce-modification of SmFeO3 thick film. Distribution of Ce particles for 5 min doping favors the adsorption of ethanol molecules as compared to other gases.
Response- Recovery Profile of the Sensor
![]() |
Figure 6: Response- recovery profiles of Ce-modified SmFeO3 sensor (dipping time 5 min) towards 60 ppm ethanol at 1000C. |
Response time is the time taken by sensor to reach 90 % of maximum response and recovery time is time taken by sensor to fall to 90 % of maximum response. Response – recovery profile for Ce-modified SmFeO3 thick film (dipping time 5 min) to 60 ppm ethanol at 100 0C was depicted in Figure. 6. Response and recovery times recorded for as prepared Ce-modified SmFeO3 thick film (dipping time 5 min) sensor were approximately 24 sec and 34 sec respectively.
Stability of Sensor
The gas response of Ce-modified SmFeO3 (dipping time 5 min) sensor to 60 ppm ethanol at 1000C was observed for the period of 90 days. Results depicted in Figure. 7 indicate good stability and durability for Ce-modified SmFeO3 (dipping time 5 min) sensor towards ethanol.
![]() |
Figure 7: Stability of Ce-modified SmFeO3 sensor (dipping time 5 min) towards 60 ppm ethanol at 100 0C. |
Ethanol Gas-Sensing Mechanism
Ethanol sensing is based on the resistance change in presence of air and then in presence of ethanol. The change in resistance depends on amount of adsorbed oxygen species on the surface of sensor and the ethanol gas species interacting with chemisorbed oxygen species. Being a p-type semiconductor, holes are the charge carriers in SmFeO3. In presence of air, there is adsorption of oxygen molecules and these adsorbed oxygen trap the electrons from the metal to form highly reactive ionic species like. The formation of oxygen species depends on temperature and expressed as follows 25

Because of this chemisorption of oxygen molecules, concentration of holes increases. Therefore, hole accumulation layer is formed near the oxide surface and it act as potential barrier between neighboring grains. As a result, sensor has small resistance in presence of air. When such sensor gets contact with ethanol, catalytic oxidation of ethanol takes place producing CO2 and H2O. The reaction occurs as follows 26.

During this desorption process, trapped electrons are returned back and the width of accumulation layer decreases. Thus there is increase in sensor resistance in presence of ethanol. The difference between these two resistances produces gas response.
Thus the present work reveals that pure SmFeO3 thick film fabricated by the screen printing technique, exhibited selective response to ethanol than other tested target gases. All Ce-surface modified SmFeO3 thick films showed improved response to ethanol. Among these Ce-modified SmFeO3 thick films, the sample with dipping time interval of 5 min exhibited excellent ethanol sensing properties such as , maximum response (16.87 at 1000C ), response time (24 sec), recovery time (34 sec), excellent stability, and good selectivity towards ethanol. Thus Ce-modified SmFeO3 can be a potential material in the fabrication of ethanol sensor. Dipping technique can be used for the surface modification of SmFeO3 thick film.
Acknowledgement
The author(s) thank VNIT, Nagpur, Maharashtra state, India for providing the facility of sample characterizations.
Conflict of Interest
The author(s) declare no conflict of interest.
Funding Sources
There is no funding sources.
References
- Gautam, Y. K.; Sharma K.; Tyagi, S.; Ambedkar, A. K.; Chaudhary, M.; Singh, P. J. Roy. Soc. open Sci. 2021, 8, 201324. https://doi.org/10.1098/ rsos.201324
CrossRef - Zhang, C.; Luo, Y.; Luo, J.; Xu, M. D. Sens. Actuators A Phys. 2019 , 289 , 118-133. https://doi.org/10.1016/j.sna.2019.02.027
CrossRef - Agrawal, S.; Rai, P.; Gatel, E.; Guell, F.; Kumar, M.; Awasthi, K. Sens. Actuator B Chem. 2019, 292, 24-31. https://doi.org/10.1016/ j.snb.2019.04.083.
CrossRef - Tian, X.; Cui, X.; Lai, T.; Ren, J.; Yang, Z.; Xiao, M.; Wang, Y. Nano Mater. Sci. 2021, 3, 390-403. https://doi.org/10.1016/j.nanoms.2021.05.011
CrossRef - Han, M. A.; Kim, H. J.; Lee, H. C.; Park, J. S.; Lee, H. N. Appl. Surf. Sci. 2019, 481, 133-137. https://doi.org/10.1016/j.apsusc.2019.03.043
CrossRef - Liu, C.; Lu, H.; Zhang, J.; Zhu, G.; Yang, Z.; Yin, F.; Wang, C. Sens. Actuator B Chem. 2018, 263,557-567.
CrossRef - Dong, C.; Zhao, R.; Yao, L.; Ran, Y.; Zhang, X.; Wang, Y. J. Alloys and Comp. 2020, 820, 153194. https://doi.org/10.1016/j.jallcom .2019.153194
CrossRef - Praveena, K.; Bharathi, P.; Liu, H. L.; Varma, K. B. Ceram. Int. 2016, 42, 13572-13585
CrossRef - Huang, H. T.; Zhang, W. L.; Zhang, X. D.; Guo, X. Sens. Actuator B Chem. 2018, 265, 443-451. https://doi.org/10.1016/j.snb.2018.03.073
CrossRef - Fan, W.; Sun, Z.; Wang, J.; Zhou, J.; Wu, K. J. Power Sources. 2016, 312, 223-233
CrossRef - Zhang, Y.; Zou, H.; Peng, J.; Duan, Z.; Ma, M.; Xin, X.; Zheng, X. Sens. Actuator B Chem. 2018, 272, 459-467. https://doi.org/10.1016/ j.snb.2018.06.007
CrossRef - Bukhari, S. M.; Giorgi, J. B. Solid State Ion. 2010, 181, 392–401. https://doi.org/10.1016/j.ssi.2010.01.017
CrossRef - Bukhari, S. M.; Giorgi, J. B. Solid State Ionics. 2009, 180, 198–204. https://doi.org/10.1016/j.ssi.2008.12.002
CrossRef - Hao, P.; Qu, G.M.; Song , P.; Yang, Z. X.; Wang, Q. Rare Mater. 2021, 40, 1651–1661 https://doi.org/10.1007/s12598-020-01672-2
CrossRef - Xue, Z.; Cheng, Z.; Xu, J.; Xiang, Q.; Wang, X.; Xu, J. ACS Appl. Mater. Int. 2017, 9 41559-41567. https://doi.org/10.1021/acsami.7b13370.
CrossRef - Pargoletti, E.; Cappelletti, G. Nanomaterials 2020, 10, 1485. https://doi.org/10.3390/nano10081485
CrossRef - Fang, S.; Peng, H.; Zhao, M.; Hu, J.; Chen, L. J. Fun. Mater. 2017, 28, 54–60.
- Niu, X.; Du, W.; Jiang, K. J. Trans. Tech. 2013, 22,5–7.
- Zhao, M.; Peng, H.; Hu, J.; Han, Z. Sens. Actuator B Chem. 2008, 129, 953–957. https://doi.org/10.1016/j.snb.2007.10.012
CrossRef - Mankar, R. B.; Kapse, V. D.; Patil, D. R. Asian Journal of Chemistry 2023, 35, 1485-1490. https://doi.org/10.14233/ajchem.2023.27874
CrossRef - Shinde, S. D.; Gaikwad, V.B.; Patil, G.E.; Kajale, D.D.; Jain, G.H. Int. J. Nano. 2012, 5, 126-135. https://doi.org/10.1504/IJNP.2012.046239
CrossRef - Maity, R.; Sakhya, A.; Dutta, A.; Sinha,T.P. Mater. Chem. and Phys. 2019, 223,78-87. https://doi.org/10.1016/j.matchemphys.2018.10.038
CrossRef - Patil, R.P.; Gaikwad,V. B.; Jain, G.H.; Gaikwad, S. S. Int. J. of Chem. and Phys Sci. 2018, 7, 259-267.
- Nahire, S.B.; Patil, G.E.; Jain, G.H.; Gaikwad, V.B.; Deshmukh, S.B. Int. J. Res. in Applied Science & Engineering Technology 2017, 9, 2535-2543.
- Patil, S. D.; Nikam,H. A.; Sharma, Y.C.; Yadav, R. S. Kumar, D.; Singh, A. K.; Patil D.R. Sens. Actuator B Chem. 2023, 377, 1-10. https://doi.org/10.1016/j.snb.2022.133080
CrossRef - Xiang, J.; Chen, X.; Zhang, X.; Gong, L.; Zhang, Y.; Zhang, K. Mater. Chem. Phys., 2018 , 213, 122–129. https://doi.org/10.1016/j. matchemphys.2018.04.024
CrossRef
This work is licensed under a Creative Commons Attribution 4.0 International License.