Polyaniline-mixed Metal (Fe-Mn-Zn) Oxide Nanocomposite Adsorbent for Removing Cu(II) ions from Aqueous Matrices
Surbhi Sankhla1, Kapil Gehlot2*
and Deshraj Sharma3
Department of Chemistry, Jai Narain Vyas University, Jodhpur, Rajasthan, India.
Department of Chemistry, Lachoo Memorial College of Science and Technology, Jodhpur, Rajasthan, India.
Department of Physics, Lachoo Memorial College of Science and Technology, Jodhpur, Rajasthan, India.
Corresponding Author E-mail: gkapil23@gmail.com
DOI : http://dx.doi.org/10.13005/ojc/390225
Article Received on : 27 Dec 2022
Article Accepted on :
Article Published : 22 Mar 2023
Reviewed by: Dr Prema K H
Second Review by: Dr. Srinath
Final Approval by: Dr. B.K Sharma
A polyaniline-mixed metal (Fe-Mn-Zn) oxide (PANFMZO) nanocomposite adsorbent is synthesized and characterized by FTIR, SEM, SEM/EDX and Brunauer–Emmett–Teller (BET) analysis. Efficiency of PANFMZO as adsorbent for removal of Cu(II) ions from aqueous matrices is analysed. The parameters like change in amount of adsorbent, contact time, pH and initial Cu(II) ion concentration are studied and removal of 69.20% of Cu(II) ion from test solution is achieved. The maximum adsorption capacity of PANFMZO for Cu(II) is found to be 75.1879 mg/g. The adsorption results are described by both Langmuir and Freundlich isotherms, the data fits better with Freundlich isotherm (R2 = 0.9998).
KEYWORDS:Adsorption; Batch Mode Technique; Nanocomposite; Polyaniline
Download this article as:
Copy the following to cite this article: Sankhla S, Gehlot K, Sharma D. Polyaniline-mixed Metal (Fe-Mn-Zn) Oxide Nanocomposite Adsorbent for Removing Cu(II) ions from Aqueous Matrices. Orient J Chem 2023;39(2). |
Copy the following to cite this URL: Sankhla S, Gehlot K, Sharma D. Polyaniline-mixed Metal (Fe-Mn-Zn) Oxide Nanocomposite Adsorbent for Removing Cu(II) ions from Aqueous Matrices. Orient J Chem 2023;39(2). Available from: https://bit.ly/3FIzjL7 |
Introduction
Copper is an essential trace nutrient; however, the excess amount is hazardous to both humans and animals.1 Due to the numerous industrial and commercial uses of copper metals and compounds2-4, copper pollution has become a significant environmental issue. The commonly employed techniques for remediation of copper ions5 from aquatic samples include chemical precipitation6, flotation7, biosorption8-10, electrolytic recovery11, membrane separation12, metal adsorption onto minerals13 and activated carbon14. The adsorption process has been extensively studied in order to solve the problem of copper ions contamination in aqueous matrices. Polyaniline-based composites, which are made by combining polyaniline with one or more similar or dissimilar materials, have been reported to be good adsorbents for removing metal ions15. Few advantages associated with them include simple synthesis, inexpensive monomer cost, good environmental stability, easily controlled reversible properties by doping, charge exchange and protonation, distinctive functional groups (e.g. NH-), and tunable properties16. The diverse morphological structures, high surface areas, good dispersibility, and synergistic features of the polymer and the filler make PANI-based nanocomposites suitable candidates for the adsorption of metal ions17. In this work, polyaniline-formaldehyde copolymer has been synthesized and employed for remediation of Cu(II) ions from aqueous matrices in the range of its toxicity limit.
Material and method
To prepare PANFMZO, 10.0 mL (100 mmol) of aniline was acidified with 12.0 mL (120 mmol) of concentrated HCl, the anilinium salt obtained was dissolved in 50.0 mL of water. 10.0 mL (100 mmol) of formaldehyde was added to the above solution and the copolymer obtained was cooled to room temperature. Aqueous solution of FeCl3.6H2O, MnCl2.4H2O and ZnCl2, in different molar ratios (Table 1) was mixed slowly in the copolymer with constant shaking over sonicating bath. Resulting mixture was treated with 10% NaOH with constant shaking for 10 min and precipitate was allowed to settle down for 45 min. The precipitate was vacuum filtered and washed until free from alkali and dried at 70 ℃ to get PANFMZO nanocomposite in powder form. 1000 ppm stock solution of Cu(II) ion was prepared by using standard method as reported18.
Table 1: Molar ratios of Fe(III), Mn(II) and Zn(II)for synthesis of PANFMZO
S. No. |
Sample |
Moles of Fe(III) ions |
Moles of Mn(II) ions |
Moles of Zn(II) ions |
1. |
S1 |
0.04 |
0.0189 |
0.0000 |
2. |
S2 |
0.04 |
0.0151 |
0.0039 |
3. |
S3 |
0.04 |
0.0113 |
0.0079 |
4. |
S4 |
0.04 |
0.0075 |
0.0119 |
5. |
S5 |
0.04 |
0.0037 |
0.0159 |
6. |
S6 |
0.04 |
0.0000 |
0.0199 |
PANFMZO was shaken with the Cu(II) ion solution in a stoppered conical flask and the concentration of residual ions was determined using AAS (ECIL, AAS4141) and the concentration of Cu(II) ion adsorbed, qe (mg/L), was determined using following equation19:
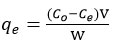
where co and ce: initial and equilibrium concentrations of adsorbate (mg/L), respectively, V: volume of solution (L) and W: mass of adsorbent (g). The percentage removal of Cu(II) ions was determined using following equation:

Results and Discussion
IR spectroscopy was employed to determine the changes in the vibrational frequencies of the groups present in PANFMZO due to adsorption of Cu(II) ion. PANFMZO before adsorption showed a peak at 3287.5 cm-1 due to secondary N-H stretch, while peak at 2791.8 cm-1 indicated formaldehyde -CH2 moiety. C-N aromatic stretch at 1338.1 cm-1 further confirmed the amine and a peak at 1599.0 cm-1 indicated C=C stretch of aromatic ring. Peak at 827.5 cm-1 appeared due to C-H out of plane bending and busy finger print region was due to substitution at 1 and 4 positions of the benzene ring (Fig.1a)20.
After adsorption, the IR spectra showed marked variation in the major peaks. The shifted peaks were observed at 3350.9 cm-1 (N-H stretch), 2899.9 cm-1 (C-H stretch; aliphatic), 1341.8 cm-1 (C-N aromatic stretch), 1587.8 cm-1 (C=C stretch; aromatic), 816.3 cm-1 (C-H bending) and changes in the finger print region were also observed (Fig 1b)21.
![]() |
Figure 1: IR spectrum of (a) PANFMZO (b) PANFMZO after adsorption |
The SEM image revealed porous structure of material with irregular shaped nanoparticles of size ranging from 72.03 nm to 133 nm (Fig. 2a). SEM-EDX analysis clearly indicated presence of only Fe, Mn, Zn and O showing the formation of the oxides of the metal ions and peak of C was due to presence of the polymer matrix (Fig 2b).
![]() |
Figure 2: (a) SEM Image (b) SEM-EDX of PANFMZO before Cu (II) ion adsorption. |
SEM image (Fig. 3a) after adsorption studies revealed rugged morphology with filled pores indicating the presence of adsorbed Cu(II) ions. This was further confirmed by SEM-EDX which showed additional peak of Cu along with Fe, Mn, Zn and O (Fig. 3b). The mapping image also provided additional evidence for the adsorption of Cu with its uniform distribution throughout the surface of PANFMZO (Fig. 3c).
![]() |
Figure 3: (a) SEM Image (b) SEM-EDX (c) SEM-EDX mapping of copper after Cu (II) ion adsorption |
From preliminary adsorption experiments, the distribution coefficient value (Kd) for samples, S1, S2, S3, S4, S5 and S6 were found to be 3502.85, 4877.45, 1584.47, 901.46, 812.71 and 632.53, respectively. Sample S2 (molar ratios Fe(III):Mn(II):Zn(II)::2.65:1.00:2.58) showed maximum Kd value and therefore was selected for further studies. The equilibrium data was calculated with the help of batch methodology22 and optimum conditions for Cu(II) ion adsorption using PANFMZO were analyzed by studying domains like variation in pH, adsorbent dose, time of contact and initial concentration of adsorbate. To examine the effect of dose, 0.01 to 0.07 g of PANFMZO was shaken with 250 mL of 1mg/L solution of Cu(II) ion. Cu(II) ion adsorption increased with rise in amount of PANFMZO up to 0.05 g (Fig. 4a) . This may be ascribed to upsurge in available adsorption sites, however, further increase in dose did not show any change due to aggregation of adsorbent23. The Cu(II) ion adsorption was also monitored by varying the contact time from 10–60 min (Fig. 4b). The initial rise in adsorption was observed with time and the equilibrium was attained after 40 min. Thereafter insignificant change in Cu(II) ion adsorption indicated that the adsorption sites are saturated with Cu(II) ions. To optimize pH conditions, Cu(II) ion adsorption studies were executed from pH 1 to 7. At pH 6, maximum adsorption was observed, at lower pH values the H+ seems to compete with metal ion for the adsorption. At pH > 6 the solution started showing precipitation which may be due to complexation of Cu(II) ions with OH– ions (Fig. 4c). The optimum initial concentration of adsorbate was also analyzed (Fig. 4d). The percentage removal of Cu(II) ions at 0.8, 1.0, 1.5, 2.0, 2.5, 3.0 mg/L was found to be 69.12%, 69.20%, 68.33%, 67.75%, 67.40% and 67.00%, respectively. The percentage removal decreases beyond 1.0 mg/L which indicated that adsorption sites are saturated beyond this concentration.
![]() |
Figure 4: Effect of (a) PANFMZO dose (b) contact period (c) pH (d) initial metal ion concentration |
The obtained data for Cu(II) ion adsorption was validated using Langmuir 24 and Freundlich isotherms25.
Langmuir isotherm was linear (Fig. 5a) with qm and RL values 75.1879 mg/g and 0.8659, respectively. The value of RL less than 1 indicated favourable adsorption of the Cu(II) ions on the adsorbent. Even the Freundlich isotherm (Fig. 5b) was found to be linear with n and Kf values being 1.0817 and 8.5704 mg/g. The n value was found to be greater than one but less than 10 indicating favourable adsorption of Cu(II) ions on PANFMZO. The R2 value for both Langmuir and Freundlich adsorption isotherm were high. Higher value of regression correlation coefficient of Freundlich model (R2 = 0.9998) indicated that adsorbed Cu(II) ions forms multilayer onto the adsorbent surface.
![]() |
Figure 5: (a) Langmuir and (b) Freundlich adsorption isotherm |
To investigate the surface area and porosity of PANFMZO, BET analysis was performed by adsorption-desorption of N2 (Fig. 6). The surface area and the average pore diameter of PANFMZO was found to be 12.06 m2/g and 43.98 Å, respectively.
![]() |
Figure 6: Nitrogen adsorption−desorption isotherm of PANFMZO |
The adsorption capacity of PANFMZO (75.1879 mg/g) is comparable to the reported values in literature as shown in Table 2.
Table 2: Maximum adsorption capacity for Cu(II) ions by different adsorbents
S. No. |
Adsorbent used for Removal of Cu(II) ions |
Adsorption Capacity qm (mg/g) |
References |
1. |
Polyaniline graft chitosan beads |
100 |
[26] |
2. |
Polyaniline/Clay nanomaterials |
22.7 |
[27] |
3 |
PANI calcium alginate |
67.95 |
[28] |
4. |
Chitosan Grafted with Polyaniline |
131.58 |
[29] |
5. |
Prussian blue/polyaniline@cotton fibers composite |
31.93 |
[30] |
6. |
Phytic acid-doped polyaniline nanofibers |
5.29 |
[31] |
7. |
Polyaniline/Ferricyanide composite |
41.625 |
[32] |
8. |
Polyanilne |
38.265 |
[33] |
9. |
Polyaniline-wheat husk composite |
95 |
[34] |
10. |
Current Study |
75.1879 |
– |
Conclusion
PANFMZO nanocomposite synthesized by the chemical oxidation method was used as adsorbent for removing Cu(II) ion in aqueous matrices. With 0.05g adsorbent dose, contact period of 40 minutes, at pH 6, and 1mg/L of Cu(II) ion concentration, 69.2% of Cu(II) ions were removed and adsorption capacity, qm of PANFMZO was found to be 75.1879 mg/g. Adsorption isotherm shows that the experimental data satisfy Freundlich isotherm better than Langmuir isotherm.
Acknowledgment
Authors acknowledge Department of Chemistry, Jai Narain Vyas University, Jodhpur and IIT Jodhpur for instrumental analysis.
Conflict of interest
Authors declare no conflict of interest for this work.
References
- Emenike, E. C.; Adeniyi, A.G.; Omuku, P.E.; Okwu, K.C.; Iwuozor, K. O. J. Water Process Eng. 2022, 47, 102715.
- Kilany, A.Y.; Nosier, S.A.; Hussein, M.; Abdel-Aziz, M.H.; Sedahmed, G.H. Sep. Purif. Technol. 2020, 248, 117056.
- Davamani, V.; Parameshwari, C.I.; Arulmani, S.; Ezra John, J.; Poornima, R. J. Environ. Chem. Eng. 2021, 9, 105528.
- Amélie, J.; Lucie, C.; Guy, M.; Jean F. B. J. Clean. Prod. 2021, 279, 123687.
- Phuengphai. P.; Singjanusong. T.; Kheangkhun. N.; Wattanakornsiri. A. Water Sci. Eng. 2021, 14, 286–294.
- Chen, Q.; Yao. Y.; Li. X.; Lu.J.; Zhou. J.; Huang. Z. J. Water Process. Eng. 2018, 26, 289–300.
- Wu, H.; Wang, W.; Huang, Y.; Han, G.; Yang, S.; Su, S.; Sana, H.; Peng, W.; Cao. Y.; Liu. J. J. Hazard. Mater. 2019, 371, 592–602.
- Dusengemungu, L.; Kasali, G.; Gwanama, C.; Ouma, K. O. Front. Microbiol. 2020, 11, 582016.
- Bashir, A.; Malik, L. A.; Ahad, S.; Manzoor. T.; Bhat, M. A.; Dar, G. N. Environ. Chem. Lett. 2019, 17, 729-754.
- Villen-Guzman, M.; Gutierrez-Pinilla, D.; Gomez-Lahoz, C.; Vereda-Alonso, C.; Rodriguez-Maroto, J. M.; Arhoun, B. Environ. Res. 2019, 179, 108849.
- Xiaoxia, Y.; Yaping, Q.; Feifan, L.; Jiancheng, S.; Zhi, S.; Shuhui, S.; Mengjun, C.; Shengyan, P. Waste Manage. 2019,95, 370-376.
- Duan, H.; Liu, H.; Hu, C.; Yang, X.; Wang, X. RSC Adv. 2020, 10,18860.
- Komy, Z. R.; Shaker, A. M.; Heggy, S. E. M.; El-Sayed, M. E. A. Chemosphere, 2014, 99, 117-124.
- Chen, W. S.; Chen, Y. C.; Lee, C. H. Processes, 2022, 10, 150.
- Eskandari, E.; Kosari, M.; Farahani, M.H.D.A.; Khiavi, N.D.; Saeedikhani, M.; Katal, R.; Zarinejad, M. Sep. Purif. Technol. 2019, 231, 115901.
- Zare, E. N.; Motahari, A.; Sillanpää, M. Environ. Res. 2018, 162, 173-195.
- Samadi, A.; Xie, M.; Li, J.; Shon, H.; Zheng, C.; Zhao, S. Chem. Eng. J. 2021, 418, 129425.
- Rice. E.W.; Baird. R.B.; Eaton. A.D.; Clesceri. L.S. Standard Methods for the Examination of Water and Wastewater 22nd Edition., 2012, 3-74.
- Primo, J.O.; Bittencourt, C.; Acosta, S.; Sierra-Castillo, A.; Colomer, J.F.; Jaerger, S.; Teixeira, V.C.; Anaissi, F.J.; Front Chem. 2020, 8, 571790.
- Pavia, D.; Lampman, G.; Kriz, G. Introduction to Spectroscopy, a Guide for Students of Organic Chemistry. 8th Indian Reprint, Brooks/Cole, Cengage Learning, 2011, 51-53.
- Ajithkumar, M.; Arivoli, S. Orient. J. Chem. 2021, 37, 1324-1328.
- Ramutshatsha, D.; Ngila, J.C.; Ndungu, P.G.; Nomngongo, P.N. Desalin. Water Treat. 2018, 104, 206–216.
- Mishra, A. K.; Shahi, V. K.; Agrawal, N. R.; Das, I.; J. Chem. Eng. Data 2018, 63, 3206– 3214.
- Wang, L.; Shi, C. X.; Wang, L.; Pan, L.; Zhang, X. W.; Zhou, J. J. Nanoscale, 2020, 12 , 4790-4815.
- Sun. H.; Xia. N.; Liu. Z.; Kong. F.; Wang. S. Chemosphere., 2019, 236, 124370.
- Igberase, E.; Osifo, P.; Ofomaja, A. J. Environ. Chem. Eng. 2014, 2 (1), 362–369.
- Soltani, H.; Belmokhtar, A.; Zeggai, F. Z.; Benyoucef, A.; Bousalem, S.; Bachari, K. J. Inorg. Organomet. Polym. Mater. 2019, 29 (3), 841–850.
- Jiang, N.; Xu, Y.; Dai, Y.; Luo, W.; Dai, L. J. Hazard. Mater. 2012, 215–216, 17–24.
- Zare, H.; Taleghani, H. G.; Khanjani, J. Int. J. Eng. Trans. B Appl. 2021, 34 (2), 305–312.
- Wang, X.; Li, Q.; Yang, D.; An, X.; Qian, X. Coatings 2022, 12 (2),138.
- Kim, H. J.; Im, S.; Kim, J. C.; Hong, W. G.; Shin, K.; Jeong, H. Y.; Hong, Y. J. ACS Sustain. Chem. Eng. 2017, 5 (8), 6654–6664.
- Ahmad Rafiqi, F.; Majid, K. J. Environ. Chem. Eng. 2015, 3 (4), 2492–2501.
- Arsalan, M.; Siddique, I.; Awais, A.; Baoji, M.; Khan, I.; Badran, M.; Mousa, A. A. A. Front. Environ. Sci. 2022, 10 (June), 1–12. 10, 895463.
This work is licensed under a Creative Commons Attribution 4.0 International License.