Glyceral Trinitrate: As Potential Corrosion Protector for Mild Steel in Acid Medium Along with Paint-Coated Steel in a Saline Environment
M. Menaga*, Sowmya Ramkumar
and D. Nalini
Department of Chemistry, PSGR Krishnammal College for Women, Coimbatore, Tamil Nadu, India.
Corresponding Author E-mail: mmenaga18@gmail.com
DOI : http://dx.doi.org/10.13005/ojc/370621
Article Received on : 10-Nov-2021
Article Accepted on :
Article Published : 21 Dec 2021
Reviewed by: Dr. Suchetan P.A
Second Review by: Dr. Syed Abuthahir
Final Approval by: Dr. Ioana stanciu
The importance of mild steel lies in its industrial applications, and the fight against corrosion is very important from an ecological, economic, technical, and aesthetic view. The current study involves the use of pharmaceutical drugs namely GTN towards corrosion inhibiting reaction was examined by gravimetric and electrochemical approaches. From weight loss studies, maximum I.E (%) 94.04% reached for 60 mg/L concentration of GTN for 6 hrs immersion time. The Polarization measurements showed that the behaviour of GTN as mixed nature and surface assimilation of GTN at the superficial, such that water molecules are substituted at the solution-metal boundary. The corrosion resistance property of the studied inhibitor as coating was also evaluated in NaCl which shows better progress corrosion retardation property of coating in the saline medium. Theoretical calculations were employed using DFT to correlate with the experimental observations.
KEYWORDS:Acid Corrosion; DFT; EIS; Epoxy resin coating; Glyceral Trinitrate; Mild steel; Polarization; Weight loss
Download this article as:
Copy the following to cite this article: Menaga M, Ramkumar S, Nalini D. Glyceral Trinitrate: As Potential Corrosion Protector for Mild Steel in Acid Medium Along with Paint-Coated Steel in a Saline Environment. Orient J Chem 2021;37(6). |
Copy the following to cite this URL: Menaga M, Ramkumar S, Nalini D. Glyceral Trinitrate: As Potential Corrosion Protector for Mild Steel in Acid Medium Along with Paint-Coated Steel in a Saline Environment. Orient J Chem 2021;37(6). Available from: https://bit.ly/3pgilM6 |
Introduction
Mild steel has excellent mechanical properties 1 and due to this property, it is used as the material of construction engineering structural material. In petroleum industries, mild steel is extensively used transmission pipelines, dubler, flow lines, etc., where it is susceptible for Oxidative degradation for which different descaling process such as acid well acidification 2-5, acid cleaning, petrochemical processes are widely used for cleaning process. Mild steel undergoes corrosion attack, due to aggressive nature [6-8] of acidic medium. This corrosive attack can be controlled by using chemical inhibitors. Organic compounds containing N,S ,O 9-10 having π electron cloud are used to protect the metals and alloys 11 extensively and these are found to be an effective corrosion inhibitors 12-13. The corrosion inhibitors forms productive coating, which avoids the chemical species from diffusing in mild steel ionization process. Drug play an important role as corrosion inhibitors due to i) low cost ii) easy solubility iii) biodegradability iv) less toxicity 14-18.
The present study deals with the determination of effectiveness of GTN (Fig.1). It is an anti-anginal drug, whose trade name is Monit-gtn 2.6mg. The main constituent of the drug is glyceryl trinitrate (GTN) with the molecular formula of C3H5N3O9. The IUPAC name of the drug GTN is 1, 3-dinitrooxypropan-2-yl nitrate.
![]() |
Figure 1: Structure of corrosion inhibitor GTN |
Experimental Work
Preparation of Materials
Size of mild steel specimens were cut into dimensions 5cm2 exposed area for gravimetric experiments, Mild steel (Weight %: 0.098 % C, 99.653% Fe, 0.02 % P, 0.012% Ni, 0.201 % Mn, 0.016% S and mild steel rod exposed surface area 1cm2 where used for electrochemical analysis. For all the experiments the surface of the mild steel samples were polished by using a separate grade (400-1000 grit) of emery papers, then cleaned by using distilled water and dried. To prepare the corrosive medium analytical grade HCl was used with proper dilution.
Preparation of inhibitor Solution
The testing stock solution of 100 mg/L of GTN was prepared by calculated amount of powdered drug was dissolved in 1M HCl solution and the desired concentrations (5 – 60 mg/L) of the GTN solution are prepared by dilution the required aliquot with double distilled water.
Methods
Weight loss method
Standard ASTM G1-03 procedure 19 was applied for weight loss measurements. Properly polished and preweighed MS ccoupons were suspended in 100ml of HCl solution using glass hooks without and with descired concentrations of GTN for 3h to 24 h. The exposed coupons were then taken out, cleaned, reweighed and the various corrosion parameters were calculated as follows.

where Wo and Wi specimen non-appearance and appearance the inhibitor.
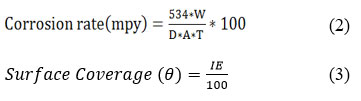
Electrochemical measurements
Mild steel rod (1cm2 area) is used working electrode, SCE as refernce and Pt electrode as counter. All potentials were measured wth respect to SCE. Before each measurement, OCP was calculated 20-21. Frequency range of EIS measurements100 KHz to 0.01 Hz 22-24 using 25 mV amplitude. Rct, Cdl determined from the plot Z’ Vs Z . From the electrochemical parameters,the I.E (%) was calculated as in the formula,
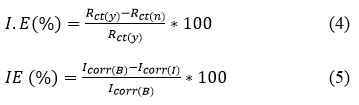
where Rct(y) , with inhibitor and Rct(n) , without inhibitor.The corrosion current densities Icorr(B) and Icorr(I) for without and with different concentration in 1M HCl.
Epoxy Coating
Materials required for preparing 5ml of paint
Volume of binder-1.25ml Zinc -2.675g
Volume of solvent-3 ml Inhibitor-0.1g
Zinc phosphate – 1g TiO2-0.4287g
Mixed well the fine powder of TiO2, zinc, inhibitor, zinc phosphate. A binder of epoxy resin is mixed with a hardener of polyamide.3ml of Xylene is used as a solvent.The mixture of epoxy resin-polyamide was added to the mixture of fine powder grained well and solvent was added drop by drop until a paint form is obtained and painted on mild steel which are was labelled as A, B and C. A-bare mild steel specimen without epoxy coating, B-Mild steel with epoxy coating (2mm thickness), C- Mild steel with epoxy coating containing GTN(2mm thickness).The coated coupons dried at 78hrs and studied in 3.5% NaCl.
Electrochemical Measurements of the paint coating mild steel
Electrochemical measurements were carried out in a similar setup of three electrode system using the epoxy coated coupons as working electrode in saline environment.
Theoretical methods
The inhibitor geometrical structure was optimized completely with the program package GAUSSIAN 09 followed by B3LYP procedure 25-27 within the basic set of 6-31G 28. All the quantum chemical parameters of electronegativity (χ), dipole moment(µ), global hardness (η), ELUMO EHOMO, Global softness (σ), ∆E, ∆N were discussed for the studied compound.
Results and Discussion
Gravimetric measurements
Based on gravimetric investigation on mild steel specimen, the stability of the inhibitor molecules was evaluated. The measurements obtained after 3h, 6h,12h and 24hrs immersion time at 298K with different concentartion of GTN (5-60 mg/L) was clearly predicted in Table 1. Thus as the inhibitor GTN concentration increases there is a increase in the I.E(%) 29-33 and corrosion rates decreases. The result shows that the metal surface are blocked by the GTN inhibitor molecules from the corrosion solution. After 6 h of immersion, I.E (91.01%) was found to decrease which may be attrributed 34-38. Metal due to prologed exposure of metal to the medium. With increased immersion time upto 24 hours there is found to be an increase in the corrosion rate 39-42. This result can be explained by the theory of adsorption.GTN molecules were desorbed, on prolonged immersion on the mild steel specimen surface, thereby increases the surface corrosive environment interaction. Moreover, the corrosion rate increases with increasing contact time, which was assigned to a small amount of GTN molecules being adsorbed in the surface to control the metal dissolution process. Hence it is clear that after 6 hours of immersion time, GTN molecules were desorbed, they turned to be ineffective as they are not involve in the inhibitive process.
Table 1: The inhibition of GTN from Gravimetric measurements.
Conc mg/L |
3 h |
6 h |
12 h |
24h |
||||
CR mm/y |
IE % |
CR mm/y |
IE % |
CR mm/y |
IE % |
CR mm/y |
IE % |
|
Blank |
1168 |
– |
1351. |
– |
3279. |
– |
6491. |
– |
5 |
601 |
48.53 |
422. |
68.73 |
1073. |
67.27 |
3378. |
47.95 |
10 |
548 |
53.06 |
296. |
78.04 |
1038. |
68.32 |
3316. |
48.91 |
15 |
492 |
57.82 |
186. |
86.18 |
714. |
78.22 |
2783. |
57.11 |
20 |
447 |
61.68 |
168. |
87.55 |
671. |
79.52 |
2526. |
61.07 |
25 |
408 |
65.08 |
151. |
88.82 |
592. |
81.94 |
2043. |
68.52 |
30 |
374 |
67.91 |
147. |
89.12 |
597. |
81.78 |
1910. |
70.57 |
35 |
307 |
73.70 |
143. |
89.41 |
551. |
83.19 |
1737. |
73.24 |
40 |
282 |
75.85 |
137. |
89.80 |
536. |
83.64 |
1722. |
73.46 |
45 |
231 |
80.16 |
131. |
90.29 |
477. |
85.45 |
1710. |
73.65 |
50 |
201 |
82.77 |
128. |
93.16 |
378. |
88.44 |
1657. |
74.46 |
55 |
169 |
85.49 |
124. |
93.78 |
314. |
90.42 |
1603. |
75.30 |
60 |
139 |
88.10 |
94. |
94.04 |
291. |
91.11 |
1462. |
77.46 |
Effect of the inhibitor concentration on protection ability over time is presented in Figure 2. It was clear from figure that at lower immersion time (3 hrs) there was a steady increase in the inhibition effeciency with concentration but for higher immersion time (6 & 12 hrs) the effeciency of the inhibitor GTN increases upto 15 mg/L concentration after which thereis not much pronouned effect inits corrosion inhibiting performace. Thus optimal concentration of GTN attaining the maximum efficiency at 15 mg/L in 1M HCl.
![]() |
Figure 2: Influence of various concentrations on the I.E of GTN for mildsteel in 1M HCl |
Potentiodynamic polarization measurements
At different concentration, the electrochemical reaction potential and current were determined from the point intersection of cathodic and anodic curves by extrapolation of linear parts of the Tafel plots. As evidenced from the Tafel plot (Figure 3) GTN affects both bc and ba. It is also proved from the change in both the tafel slopes values which proves that GTN inhibitor behaves with mixed nature. I.E(%), it reaches maximum efficiency 85.7% at 60mg/L (Table 2). This results indicates that the GTN inhibitor, surface of the metal active sites are blocked and formed by a barrier between the charge transfer and mass which are the evidences fort he decrease in the interaction oft he metal surface with the corrosive environment.
![]() |
Figure 3: Polarization curves observed for mild steel electrode in 1M HCl including addition concentrations of GTN. |
Table 2: Polarization parameters for the corrosion of mild steel without and with various concentrations of GTN in 1M HCl.
Concentration mg/L |
Ecorr mV |
Icorr μA/cm2 |
IE % |
bc mV/dec |
ba mV/dec |
Rp Ω cm2 |
IE % |
Blank |
-543 |
217 |
– |
101 |
117 |
108 |
– |
5 |
-525 |
130 |
40.09 |
76 |
146 |
166 |
34.94 |
15 |
-525 |
75 |
65.44 |
91 |
136 |
314 |
65.61 |
30 |
-529 |
54 |
75.12 |
86 |
139 |
430 |
74.88 |
45 |
-529 |
45 |
79.26 |
81 |
135 |
469 |
76.97 |
60 |
-529 |
31 |
85.71 |
82 |
137 |
492 |
78.05 |
Electrochemical impedance spectroscopic measurements
From Figure 4 and Table 3, the experimental curves are best fit and the electrochemical parameters are obtained. The results shows that as inhibitor concentration increases there is an increase in the Rp and decreases in Cdl 43. Rp values are increases with inhibitor concentration designates growth in the θ, causing the inhibition efficiency increases 44-46
![]() |
Figure 4: Nyquist plots for mild steel corrosion in 1M HCl without and with GTN Concentrations |
Table 3: EIS paprameters for mild steel in HCl with GTN
Concentration mg/L |
RS Ω cm2 |
Rct Ω cm2 |
IE % |
Cdl μF/cm2 |
θ |
Blank |
6.81 |
19 |
– |
12.9 |
– |
5 |
9.23 |
45 |
58.04 |
26.4 |
-1.0465 |
15 |
16.6 |
68 |
72.42 |
23 |
-1.0465 |
30 |
16.1 |
107 |
82.40 |
19.1 |
-0.7829 |
45 |
19.2 |
114 |
83.39 |
18.2 |
-0.4806 |
60 |
20.3 |
135 |
86.03 |
17.5 |
-0.4109 |
Because the adsorption of the inhibitor molecule increases with increased concentration, the Cdl value lowers, indicating that the contact of the metal surface area with the medium reduces. The interface layer is affected by the increased substitution of water at the solution-metal border, which decreases the dielectric constant value 47-51. The shift in the Cdl value, which corresponds to the decrease in the amount of the metal deterioration, is a proof for the displacement of water at the interface double layer. The superficial heterogeneity is represented by constant n values. The n rate increases, indicating that the surface of mild steel becomes more and more homogeneous as the inhibitor concentration rises due to the increased surface coverage.
Epoxy coating behavior of GTN in 3.5% of NaCl
Figure 5 depicts an equivalent circuit model of the cell system. It was used to fit curves and determine the resistance and coating capacitance of epoxy coating systems. Rt – charge transfer resistance, CPEcoat – coating capacitance, Rs – solution resistance, Rcoat – coating resistance, CPEdl – dobl elayer capacitance.
![]() |
Figure 5: Combining the EIS data with the Euivalent circuit model |
From the figure 6, Nyquist plot for the coating in 3.5 percent NaCl was investigated. The coatings investigated show a larger capacitive loop in the Nyquist plots at first, with the dielectric response matching that of the coating 52-53. The coating acts as a barrier layer and has a high coating resistance (Rcoat)54. The impedance spectroscopy shows only one gradually diminished capacitive arc after a few hours of immersion, indicating ongoing penetration of the electrolyte solution and little electrochemical processes. In addition, the coating’s macroscopic appearance remains unaffected. Because the mass transfer pcorrosion mechnaism is impeded in presence of GTN, a diffusion tail forms in the impedance spectroscopy as the immersion time increases.
![]() |
Figure 6: Nyquist plot of epoxy coated mild steel coupons in NaCl (a) 0 hours, (b) 48 hours, and (c) 168 hours |
Table 4: Electrochemical impedance characteristics for paint coated mild steel corrosion in NaCl
Sample Name |
Ageing period (hours) |
Rs (Ω cm2) |
Cdl (mF/cm2) |
Rcoat (Ω cm2) |
Rt (Ω cm2) |
Rtot (Ω cm2) |
Bare Mild Steel |
0 |
8.1 |
9 x 10-7 |
3922 |
-3849 |
73 |
48 |
7.3 |
9 x 10-7 |
-8.54 |
7.4 |
-1.1 |
|
168 |
9.6 |
1.13 x 10-5 |
-31.4 |
29 |
-60.4 |
|
Epoxy coated mild steel |
0 |
22.2 |
132 |
939 |
151 |
1090 |
48 |
26.4 |
9 x 10-7 |
804 |
-7535 |
499 |
|
168 |
33.8 |
9 x 10-7 |
-176 |
168 |
-8 |
|
Epoxy coated mild steel with GTN |
0 |
58 |
118 |
1830 |
285 |
2115 |
48 |
48 |
571 |
1217 |
98 |
1315 |
|
168 |
59 |
9 x 10-7 |
-5665 |
6012 |
347 |
Corrosion in NaCl
Potentiodynamic polarization studiesin 3.5% of NaCl
As illustrated in Figure 7, the potentiodynamic polarisation plots reveal the favourable effect of paint coating when compared to bare MS (A), epoxy coated MS (B), and epoxy coated MS including the inhibitor (C) in a saline environment. The electrochemical characteristics of the corrosion process, Ecorr, Icorr, ba & b care given in Table. 5 shown. (ba,bc). The corrosion potentials on painted mild steel surfaces moved to lower negative values, and the anodic current densities on these surfaces were lower than on polished mild steel surfaces 55. These findings can be taken as demonstrating that an epoxy-coated steel surface is more corrosion resistant than an untreated steel surface. This study demonstrates a significant improvement in corrosion resistance coating. The resistance was determined to be low on the seventh day.
![]() |
Figure 7: Tafel plot of painted coupons in NaCl (3.5%) at (a) 0 hr (b) 48 hrs (c) 168 hrs |
Table 5: Parameters of potentiodynamic epoxy coated coupons in NaCl (3.5%)
Sample |
Ageing period (hours) |
Ecorr (mV)
|
Icorr (µA/cm2)
|
ba (mV/dec)
|
bc (mV/dec)
|
A |
0 |
-634 |
190 |
481 |
126 |
48 |
-647 |
9.92 |
299 |
118 |
|
168 |
-638 |
16 |
142 |
161 |
|
B |
0 |
-647 |
9.92 |
299 |
118 |
48 |
-693 |
66 |
122 |
287 |
|
168 |
-595 |
21 |
155 |
121 |
|
C |
0 |
-638 |
16 |
142 |
161 |
48 |
-608 |
18 |
9 |
155 |
|
168 |
-738 |
27 |
84 |
208 |
Quantum chemical Studies
Frontier molecular orbitals (HOMO, LUMO) is the calculation form of quantum chemical studies. It is used to relate the inhibition efficiency and the molecular structure of the inhibitor 56-59. Figure 8 represents the charge distribution of the GTN inhibitor. The electron donating and electron accepting ability is related to energies of frontier molecular orbitals in a molecule. Figure 9 a & b represents the EHOMO and ELUMO of the inhibitor molecule
![]() |
Figure 8: Charge distribution structure of GTN |
![]() |
Figure 9: (a). The GTN’s HOMO |
![]() |
Figure 9: (b). The GTN’s LUMO |
From Table 6, quantum chemistry parameters that are arrangement molecules’ well-known minimal energy configuration. High EHOMO values 60 indicate a molecule that has a proclivity for donating electrons to the Fe atom’s vacant d orbital 61-62. The high value of HOMO, -11.99 eV, and the very low value of LUMO, -1.80 eV, corresponding to the value of HOMO, -11.99 eV, and the very low value of LUMO, -1.80 eV, corresponding to the value of E (10.19 eV), have an insignificant value, indicating that the energy required for electron elimination, resulting in good inhibition efficiencies and a better dipole moment. The dipole value of 4.677 eV indicates that the investigated inhibitor system has good adsorption characteristics on the metal surface.
Global Hardness η are important pointer of a molecules tendency concerning covalent interaction, softness are accelerate the surface and molecules interaction as well as the metal state and hybridization 63. From Table 6 visibly η have lower values (5.09eV) that indicates the high corrosion inhibition potential of GTN. Global softness (σ) is 0.09 eV. According to Lukovis et al, a N value of less than 3.6 implies that GTN has a stronger potential to donate electrons 64. The electron-donating capacity of GTN is confirmed by the same order of N and EHOMO.
Table 6: Quantum chemical parameters obtained by DFT calculation
Quantum chemical Parameters |
GTN |
Molecular Formula |
C3H5N3O9 |
Total Energy (a.u) |
-947.36 |
EHOMO (eV) |
-11.99 |
ELUMO (eV) |
-1.80 |
∆E (eV) |
10.19 |
Dipole Moment (µ) (eV) |
4.677 |
Global Hardness (η) (eV) |
5.09 |
Global Softness (σ) (eV) |
0.09 |
Electronegativity (χ) (eV) |
6.89 |
∆N |
0.1 |
Conclusion
The inhibitive nature of a pharmaceutically active chemical, glyceryl trinitrate GTN, against acid corrosion and as an epoxy coating protection in a salty environment was investigated using the following data.
In 1M HCl, the pharmaceutically active chemical glyceryl trinitrate GTN inhibited mild steel corrosion, and notable efficiency increase when noted for incremental change in inhibitor concentration.
The inhibitive action was attributed to the inhibitor molecule after becoming physically adsorbed. The Langmuir isotherm governs the adsorption process.
The mixed type nature of GTN in acid media is demonstrated by its polarisation behaviour.
Impedance studies of paint coating in 3.5 percent NaCl demonstrate that including GTN into the paint improves the performance of the coating, resulting in a coating with strong antipermiability resistance. It’s also worth noting that, thanks to these new refined passivation methods, the produced epoxy coatings with GTN might save the a lot money.
Inhibitive impact examined substances was connected with data derived from DFT calculation. Both experimental and theoretical calculations coincide well.
Acknowledgement
The authors express their gratitude to PSGR Krishnammal College for Women, DST-FIST, UGC, for the financial support providing the essential facilities.
Conflict of interest
There are no conflicts of interest declared by any of the authors
Funding Sources
There are no funding source.
References
- Veedu, K.K.; Kalarikkal, T.P.; Jayakumar, N.; Gopalan, N.K.; ACS Omega, 2019.4, 10176–10184
CrossRef - Sowmya Ramkumar; Mumtaz, Nalini, D.; Eno, A.Q.; J. Heterocycl. Chem., 2019.,1–17
CrossRef - Mohan, R.; Joseph, A.; Egypt. J. Pet., 2018, 27, 11–20
CrossRef - Liao, L.L.; Mo, S.; Luo,H.Q.; Feng, Y.J.; Yin,H.Y.; Li, N.B.; Corros. Sci., 2017, 124, 167–177
CrossRef - Ouknin, M.; Romane, A.; Ponthiaux, J.; Costa, J.; J.of Corrosion reviews, 2020, 38
CrossRef - Ben, M.; Abubshait, S.; Etteyeb, N.; Kamoun, M.; Arab. J. Chem., 2020,13, 4846–4856,
CrossRef - Mobin, M.; Zehra, S.; Aslam, R.; RSC Adv.,2016 ,6, 5890–5902,
CrossRef - Nwankwo, H.U.; Olasunkanmi, L.O.; Ebenso, E.E.; Sci. Rep., 2017, 7, 2436
CrossRef - K. Azzaoui K.; Corros. Sci., 2017,129, 70–81, 2017.
CrossRef - Zheng, X.; Zhang, S.; Gong,M.; Li,W.; Ind. Eng. Chem. Res.,2014 ,53, 16349–16358,
CrossRef - Bendaif, H.; Melhaoui, A.; AzzouziM, El.; Legssyer, B; Hamat, T; Elyoussf, A.; Aouniti, AE.; Ouadi, Y.; Aziz, M.; J Mater Environ Sci , 2016,7,1276–1287.
- Verma, C.; Olasunkanmi, LO.; Ebenso, EE.; Quraishi, MA.; Obot, IB.; J Phys Chem C , 2016, 120, 11598–11611 .
CrossRef - Verma, C.; Olasunkanmi,OIB.; Ebenso, EE.; Quraishi, MA.; RSC Adv, 2016, 6,1–50
CrossRef - Alan Miralrio , Araceli Espinoza Vázquez A.; J.of Process,” 2020. 8, 942
CrossRef - Fouda, A.S.; Ibrahim, H.;. Rashwaan, S.; Ahmed, R.M.; 2018, 13,. 6327–6346.
- As, F.;. Ma, E.M.; El, T.; 2017 , 5, 1–8,
- Abeng F.E.; Valentine, A.C.; 2020.
- Diki,N.; Silvère, Y.; Valery, B.K.; Guy-richard, M.; Augustin, O.; 2018,11, 24–36
- ASTM G1-03, “Standard practice for preparing, cleaning and evaluating corrosion test specimens”, ASTM International, West Conshohocken, USA (2003).
- Gurudatt, D.M.; Mohana, K.N.; Ind. Eng. Chem. Res., 2014, 53, 2092–2105
CrossRef - A. E. S. Fouda, A.E.S.; El-maksoud,S.A.A.;. El-sayed, E.H.; 2021,. 13497–13512
CrossRef - Mirzakhanzadeh, Z.; Kosari, A.; Moayed, M.H.; Naderi,R.; Taheri,P.;. Mol,J.M.C.; Corros. Sci., 2018, 138, 372–379,
CrossRef - Mishra, A.; Verma, C.; Lgaz,H.; Srivastava, V.; Quraishi, M.A.;. Ebenso,E.E.; J. Mol. Liq.,2018 , 251,. 317–332,.
CrossRef - Ansari, K.R.;. Quraishi,M.A.; Singh, A.; Ramkumar,S.; Obote,I.B.; RSC Adv.,2016, 6, 24130–24141,
CrossRef - Abdallah, M.; El Defrawy, A.M.;. Zaafarany, I.A.; Sobhi, M.;. Elwahy, A.H.M.; Shaaban, M.R.; Int. J. Electrochem. Sci., 2014, 9, 2186–2207,
- Kathirvel, K.; Thirumalairaj, B.; Jaganathan, M.; Open J. Met., 2014, 04, 73–85, 2014
CrossRef - Momeni, M.J.; Behzadi, H.; Roonasi, P.; Sadjadi, S.A.S.; Mousavi-Khoshdel, S.M.; Mousavi,S.V.; Res. Chem. Intermed.,2015, 41, 6789–6802.
CrossRef - Ansari, K.R.;. Quraishi,M.A.; Singh, A.; Sowmya Ramkumar; Obote,I.B.; RSC Adv.,2016, 6, 24130–24141,
CrossRef - Li, X.; Arab. J. Chem., 2014.
- Prabhu,R.A.; Venkatesha,T.V.; Praveen,B.M.; Chandrappa,K.G.; Hamid,S.B.A.;2014 , 67, 675–679.
CrossRef - Gaaz, T.S.; Takriff, M.S.; 2020,1–8.
- Abeng,F.E.;. Anadebe, V.C.; Nkom,P.Y.; Uwakwe,K.J.;. Kamalu,E.G.; 2021,11, 11–26
- Ogunleye O.O.;Arinkoola,A.O.;Eletta O.O.;Agbede, Y.A,Osho.;Morakinyo.A.F,;hamed,J.O.; 2020, 6, e03205,
CrossRef - Tourabi,M.; Nohair, K.; Nyassi,A.; Hammouti,B.; Jama,C.; Bentiss,F.; J. Mater. Environ. Sci., 2014,5, 1133–1143
- Bammou , L.; Belkhaouda1 , M.; Salghi, R..; Benali O.;,. Zarrouk ,A.; Al-Deyab4 , S.S.; Warad, I.; , Zarrok, H.;. Hammouti ,B.;Int. J. Electrochem. Sci.,2014, 9, 1506–1521,
- Iroha N.B.; Nnanna,L.A.; 2019, 10, 898–908,
CrossRef - Fouda, A.S.; Hassan,A.F.; Elmorsi,M.A.;. Fayed, T.A.; Abdelhakim,A.;,Int. J. Electrochem. Sci.,2014, 9,. 1298–1320.
- kosari,A.;Moayed,M.H.;Davoodi ,A.;Parvizi,R.;Momeni ,M.;Eshghi H.;Moradi,H.;Corros. Sci., 2014.; 78, 138–150,
CrossRef - Hameed, R.S.A.; Al, E.A.I.H.I.; Mohamed, S.; J. Bio- Tribo-Corrosion,. 1–10, 2020.
- Arockiasamy,P.; Sheela, X.Q.R.; Thenmozhi,G.; Franco,M.;. Sahayaraj,J.W.;. Santhi,R.J.; International journal of Corrosion,2014,
CrossRef - Ahmed, R.A.; Farghali,A.;. Fekry,A.M.;,Int. J. Electrochem. Sci.,2012, 7, 7270–7282.
CrossRef - Zaafaranya,I.A.;Hamza A.Ghulman,Int. J. Corros.,2013,2,82-161
CrossRef - Ansari,K.R.;Sowmya Ramkumar.;Nalini,D.; Quraishi,M.A.; Cogent , 2016, 2,1145032
CrossRef - SeikhA.H.; Sherif, E.M.;. 10, 895–908,
- Taylor,P.;. Ghasemi,O .; Danaee,I.; Rashed,G.R.; Avei,M.R.; Maddahy,M.H.;2015, 37–41
- Khelifa,A.; Hamitouche, H.; Khadraoui,A.; Hadj Ziane, A.; J. Mater. Environ. Sci., 2015, 6, 1890–1895
- Khadiri,A.; Saddik,R.; Bekkouche,K.; Aouniti,A.; Hammouti, B.; Benchat, N.; J. Taiwan Inst. Chem. Eng.,2015, 000, 1–13
- Sowmya Ramkumar; Nalini, D.; Mater. Today Proc.,. 2019,18, 1696–1708
CrossRef - Hamdan ,A.B.;Suryanto,.;Haider, F.I;1,J. Mater. Environ. Sci., 2014, 5, . 767–778
- Barba,V.; Ríos, J. P. F. L , Casales,M.; 2021,
- K. R. Ansari,K.R.; Sowmya Ramkumar,S.; D. Nalini,D.; and M. A. Quraishi, M.A.;“ Cogent Chem.,2016, 2,
CrossRef - Qi,K.;. Sun,Y.; Duan,H.;. Guo,X.; Corros. Sci., 2015,98, 500–506.
CrossRef - Sowmya Ramkumar,; Nalini, D.; oriental journal of chemistry, 2015, 31, 1057-1064
CrossRef - Z. Chen,Z.; C. He,C.; F. Yu,F.; Wang, Y.;2017, 12, 2798–2812
- Rajasekharan, V.; Stalin,T.; Viswanathan,S.; Manisankar,P.;2013, 8, 11327–11336,
- Hadisaputra,S.; Hamdiani,S.;. Purwoko, A.A.; J. Appl. Chem. Sci., 2017, 312–317,
CrossRef - Sowmya Ramkumar,; Nalini, D.; oriental journal of chemistry, 2015, 31, 1057-1064
CrossRef - Al-amiery,A.;. Salman,T.A.; Alazawi,K.F.;. Shaker,L.M.; KadhumA.A.H.;, Takriff,M.S.; 2020,202–209
CrossRef - Eldesoky,A.M.;. Diab, M.A., El-Bindary, A.A.; El-Sonbati, A.Z.; Seyam,H.A.; J. Mater. Environ. Sci., 2015,. 6, 2148–2165
- Sowmya Ramkumar,; Nalini, D.; oriental journal of chemistry, 2015, 31, 1057-1064
CrossRef - A. Mishra A.; Ankusg Mishra.;Chandrabhan verma.;Srivastava, V.;Lgaz,H.;Quraishi,M.A.;Eno.E.Ebenso, , J. Bio- Tribo-Corrosion, 2018,. 4, 0.
CrossRef - Junaedi,S.; Al-Amiery,A.A.; Kadihum, A.;. Kadhum, A.A.H.; Mohamad,A.B.; Int. J. Mol. Sci., 2013,14, 11915–11928.
CrossRef - Ansari, K.R.; Quraishi, M.A.;Ambrish singh.; Sowmya Ramkumar,;Obote,B,;RSC Advances,2016,6, 24130-24141
CrossRef - Zohdy , K.M.; Rabab, M.; El-Sherif , Sowmya Ramkumar , El-Shamy, A.M.; EL Upstream Oil and Gas Technology ,2021,6,
CrossRef
This work is licensed under a Creative Commons Attribution 4.0 International License.